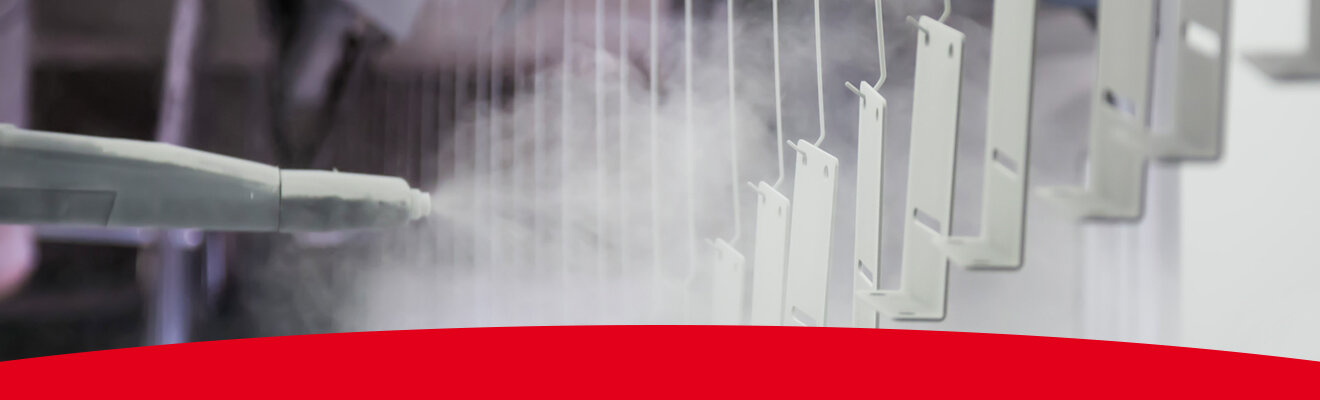
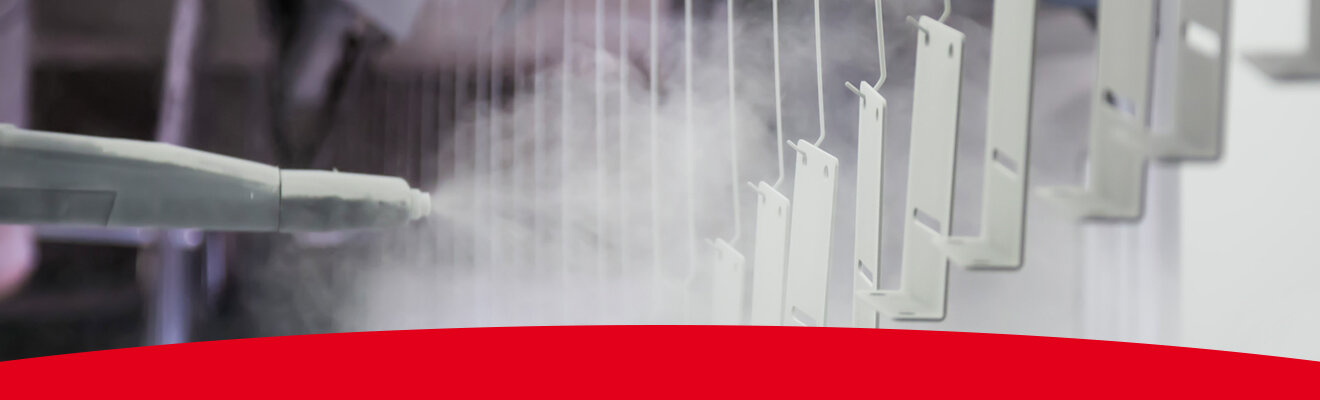
Unveiling the Science Behind ESD Powder Coating: Shielding Sensitive Electronics from Static Hazards
To combat this challenge, industries have turned to innovative solutions such as ESD powder coating. This advanced technology offers a dynamic way to prevent the accumulation and discharge of static electricity, safeguarding electronic equipment and components from harm.
As we explore the science behind ESD powder coating, it's equally important to examine how the need for these specialized benches compares to using ESD mats on non-ESD powder-coated benches.
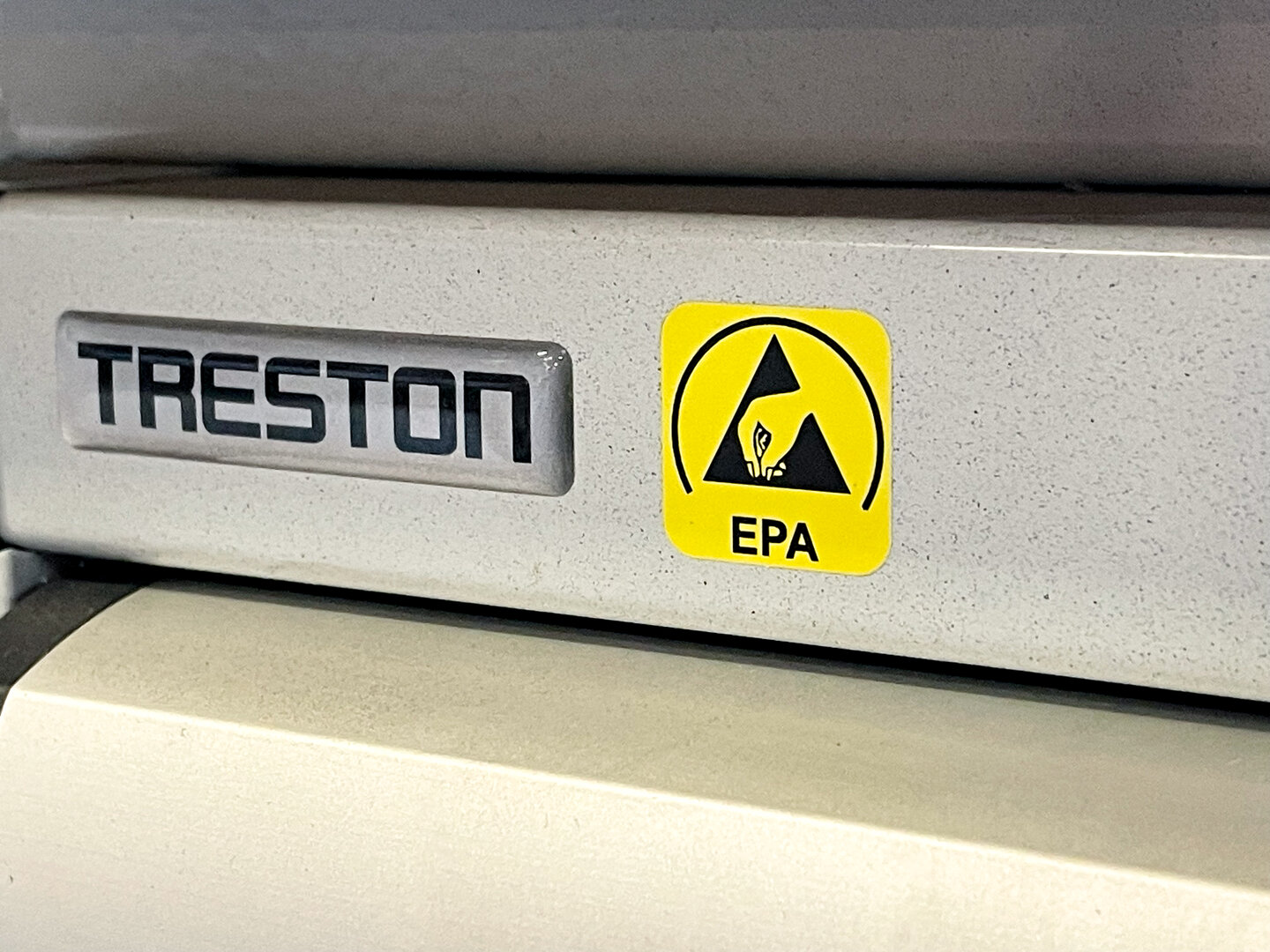
Effective Methods for Protecting Workstations from Static Discharge
Several methods exist to shield workstations from static discharge, including the use of ESD mats, ESD laminate surfaces, and ESD powder-coated workstations.
Method 1: ESD Mats on Non-ESD Powder-Coated Benches
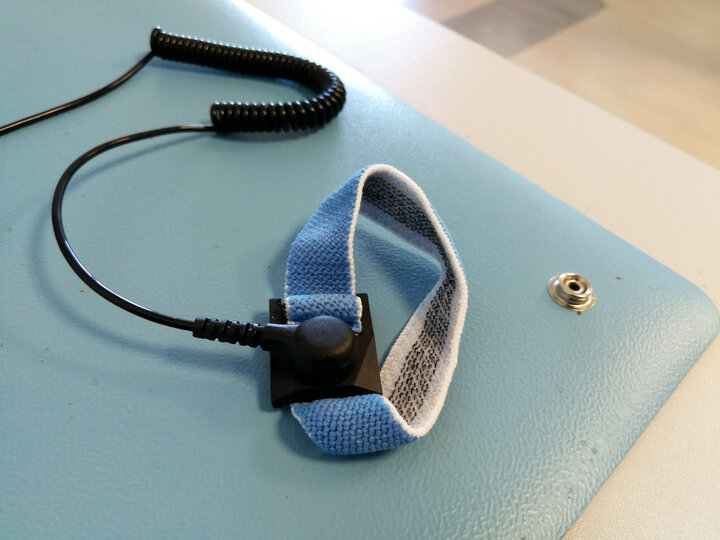
ESD mats have been a go-to solution for creating a grounded surface that dissipates static charges. These mats are made of conductive materials and are placed on workbenches to provide a pathway for any accumulated charges to flow harmlessly to the ground. While effective, they come with certain limitations.
Non-ESD powder-coated benches, while providing a robust work surface, lack the specific properties required to dissipate static charges. In this case, facilities utilize an ESD mat on the worksurface. However, this can lead to several challenges:
- Limited ESD Protection: Although ESD mats offer a layer of protection, they are not as comprehensive as ESD powder-coated benches. They primarily focus on the work area's surface, leaving other parts of the bench and equipment susceptible to static buildup. Static charge generates an electric field around the framework, which is hazardous in an EPA area.
- Maintenance Challenges: Despite regular and proper cleaning, ESD mats have a limited lifespan. Over time, they are prone to fraying or damage, necessitating timely replacement to maintain effective ESD control. It's crucial to plan these replacements carefully to avoid disruptions in workflow.
- Inconsistent Coverage: Placing ESD mats on non-ESD powder-coated benches might provide localized protection. However, the overall bench structure may still harbor static buildup, leading to potential discharge events on uncoated sections.
Method 2: ESD Work Surfaces on non-ESD Powder-coated benches
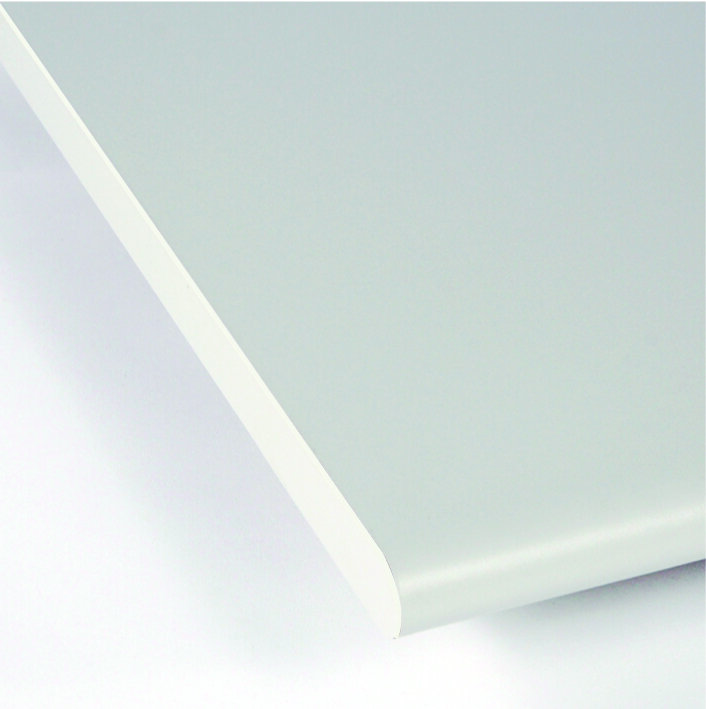
Using ESD laminate tabletops on a standard, non-ESD painted workstation can provide benefits:
- Effective ESD Protection: They provide a reliable path-to-ground, significantly reducing the risk of static damage to electronic components.
- Consistent Performance: The impregnated conductive structure ensures uniform dissipation of static charges across the entire surface.
- Durability: These tabletops are generally robust and long-lasting, capable of withstanding the rigors of a typical industrial environment.
- Safety: By effectively managing static discharge, they enhance the overall safety of the workspace, particularly in areas dealing with sensitive electronics.
ESD laminate can also be used as a shelving material. Grounding of laminate surfaces requires additional ground wiring for each.
For ensuring complete ESD protection for sensitive electronic components, let’s look at another method – ESD Powder Coating.
Understanding ESD Powder Coating
ESD powder coating is a specialized finishing process applied to surfaces that require protection against electrostatic discharge. It involves applying a layer of conductive or dissipative powder to a substrate, such as metal, using a combination of electrostatic attraction and heat curing. The primary goal of this coating is to create a controlled path for the dissipation of electrical charges, ensuring that any built-up static electricity does not harm nearby sensitive components.
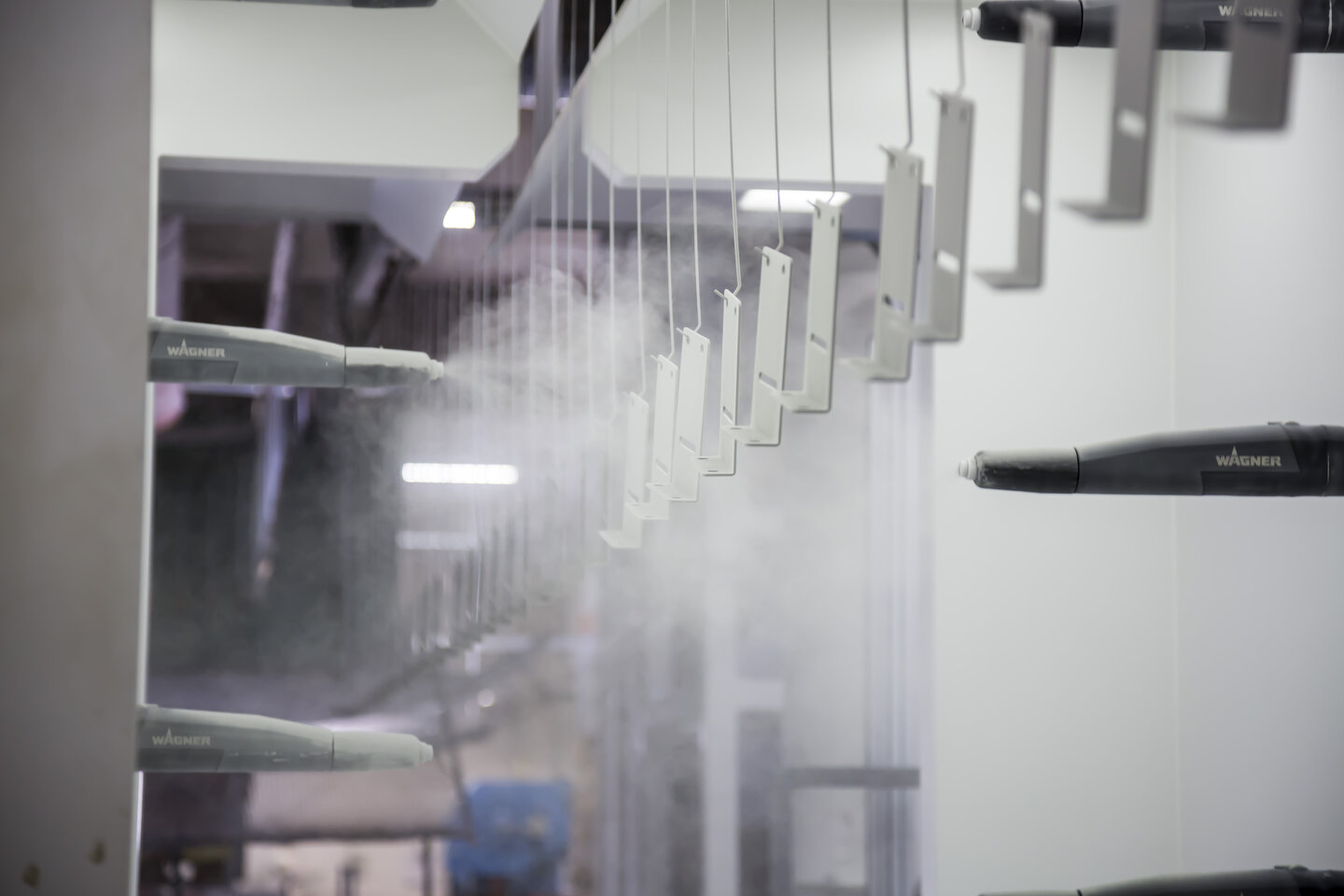
How ESD Powder Coating Works
- Powder Formulation: ESD powder coatings are formulated with a blend of conductive or dissipative materials, which allow the coating to carry electrical charges and facilitate their controlled movement. These materials can include carbon black, carbon fibers, and other conductive additives.
- Preparation: Before applying the ESD powder coating, the substrate is cleaned and prepared to ensure proper adhesion. Any contaminants, oils, or residues that might hinder the coating's performance are removed.
- Electrostatic Application: The ESD powder coating is applied using an electrostatic spray gun. The powder particles are charged with an electric charge opposite to that of the substrate. This creates a strong attraction between the charged particles and the grounded substrate, ensuring an even and precise coating.
- Curing Process: Once the ESD powder coating is applied, the coated substrate is placed in an oven for curing. The curing process involves heating the coated surface to a specific temperature that causes the powder particles to melt and fuse together. This results in a continuous, seamless coating that adheres firmly to the substrate.
- Electrostatic Dissipation: The key feature of ESD powder coating is its ability to facilitate the controlled dissipation of electrical charges. When a static charge is present on the coated surface, the conductive or dissipative materials within the coating provide a pathway for the charge to flow safely to the ground. This prevents the accumulation of high voltages that could potentially damage nearby electronic components.

ESD powder coating stands out for its ability to effectively dissipate static charges, offering robust protection against electrostatic discharge. These coatings are durable, resistant to wear, chemicals, and environmental factors, making them suitable for various industrial applications. They can be applied to a range of substrates like metals, plastics, and wood, and customized in color and finish for aesthetic appeal.
Additionally, being typically solvent-free, ESD powder coatings are a more environmentally friendly choice, reducing the emission of harmful volatile organic compounds.
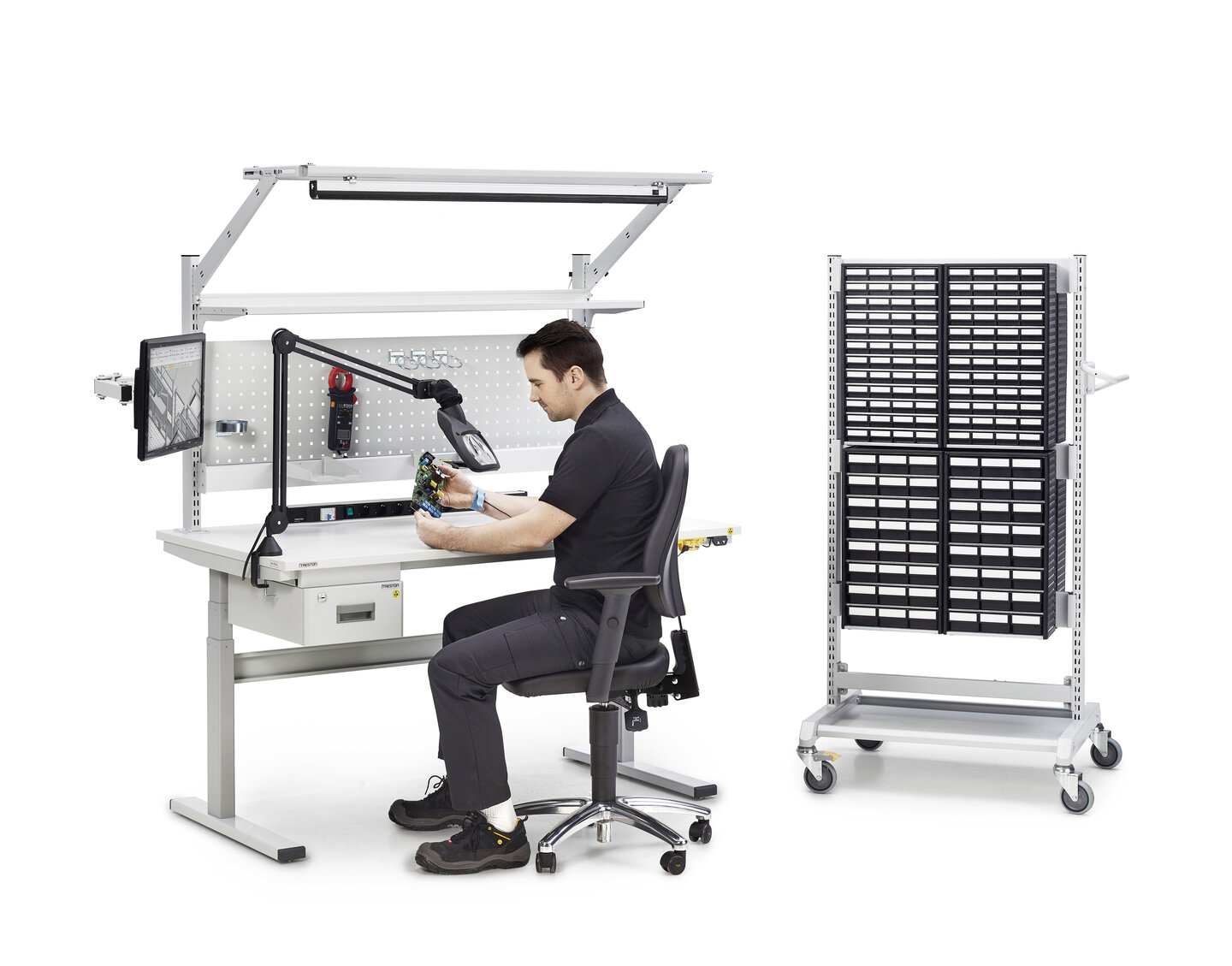
The Advantages of Using ESD Powder-Coated Work Benches
ESD powder-coated steel benches offer a comprehensive solution that goes beyond the capabilities of ESD mats or ESD laminate on non-ESD benches:
- Holistic ESD Protection: ESD powder-coated benches are designed to provide complete ESD protection across the entire workstation. The specialized coating creates a controlled path for static charge dissipation, ensuring that the entire workspace remains free from harmful charge buildup. This applies to all parts of the workstation, from bench frame to shelving and bin rails.
This animation represents the dissipation of an electric charge across the surface of an ESD powder coated surface. Carbon flecks in the paint help to protect sensitive electronic components from damage caused by static discharge. - Consistency and Durability: Unlike ESD mats that require regular maintenance to retain their conductivity, ESD powder-coated benches offer consistent and durable ESD protection. The coating remains effective over time, without the need for frequent cleaning or replacement.
- Integrated Solution: ESD powder-coated benches are purpose-built with ESD protection in mind. They offer a seamless integration of ESD properties, ergonomic design, and structural durability, catering to the unique needs of modern work environments.
- Minimized Disruption: ESD powder-coated benches provide continuous protection without the need for additional ESD mats or frequent repositioning. This minimizes disruption to workflow, ensuring a smoother and more productive operational process.
- Single Grounding Point: With ESD powder-coated benches and accessories, grounding the frame is all that is needed, eliminating the need to ground workstation accessories, such as shelves or bin rails.
Choosing the Right Solution
While ESD mats have their place in certain scenarios, ESD powder-coated benches, paired with an ESD work surface, offer a more robust and comprehensive solution for industries that demand rigorous ESD protection. The ability to integrate ESD properties directly into the painted steel, combined with the ergonomic and structural benefits of these benches, makes them a clear choice for enhancing both workplace safety and efficiency.
ESD powder coating is a sophisticated technology that plays a crucial role in safeguarding sensitive electronic equipment and components from the risks associated with electrostatic discharge. By creating a controlled pathway for the dissipation of electrical charges, this innovative coating technology contributes to enhanced product reliability, reduced downtime, and increased operational efficiency across a variety of industries.
Did you know?

Learn more about ESD control from our short explainer video:
Treston's range of standard and stocked painted products come with a light grey ESD powder coating, providing efficient ESD control without any extra cost or extended lead time. This ensures that our customers have immediate access to effective ESD solutions.
Feel free to explore our comprehensive selection of ESD products by clicking the link below.