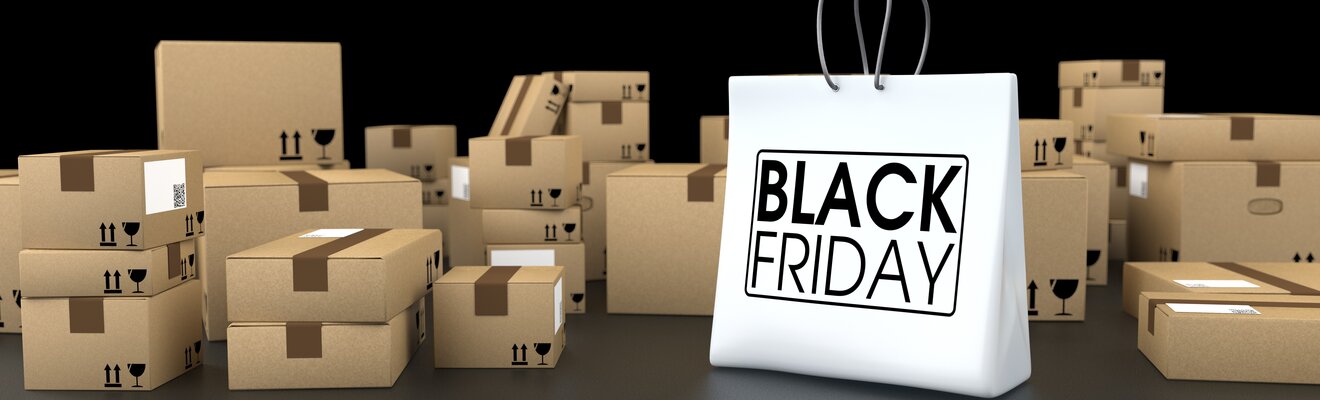
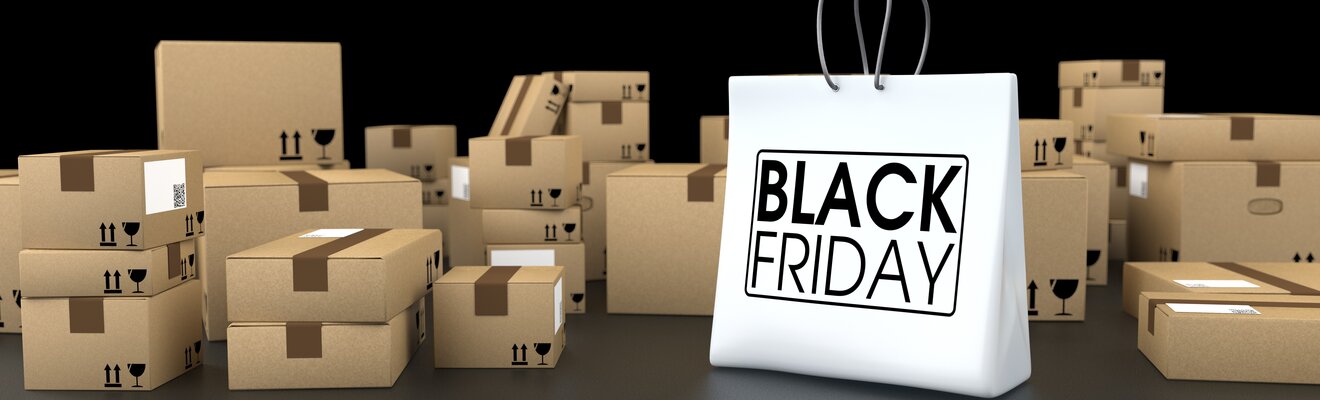
How To Prepare A Packing Facility For Black Friday 2020
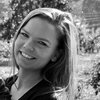
Carissa Harris
For the shipping industry, the week of Black Friday is always the busiest time of the year. It’s also the most crucial. In 2019, 93.2 million people ordered something online on Black Friday. On Cyber Monday of 2019, total sales escalated by 19% compared to the previous year with $9.4 billion worth of online transactions being made. While this is fantastic news for online retail stores, this puts packing facilities in a tight spot. Due to the COVID-19 pandemic, economists are estimating that the year-over-year growth of online sales on Black Friday 2020 will massively overshadow that of previous years. With online sales growing so rapidly each year, what can packing facilities do to keep up with the unprecedented increase in volume?
Setting Up A Packing Facility Based On Lean Principles
In order to stay on top of the huge swell in packages that need to be packed, shipped, and handled, operations need to emphasize lean principles in their processes and physical layout. Lean principles stress that productivity can be maximized by eliminating waste. The lean methodology identified seven types of waste, including transportation, inventory, motion, waiting, over processing, overproduction, and defects. While the lean methodology was originally designed for manufacturing operations, it can be modified to help packing operations reduce waste to improve speed and accuracy, and ultimately increase profits via improved throughput.
Critically Examine Processes To Identify Where There Is Waste—Then Eliminate It
In the packing industry, there are numerous ways that waste can manifest and result in profit loss. Look for bottlenecks in your process. Are packers able to move products through each step of the order fulfillment process, or are there points at which the process is unnecessarily slowed down? What about for your material handling process? Can the items get to your packing stations in a fast, seamless manner? Replacing bottlenecks with more fluid steps in the process can help increase efficiency significantly.
Building in steps that reduce the possibility of an error occurring further downstream can also help improve productivity. Identify where mistakes often occur and think about where quality assurance steps can be added. Rearrange workstations to include spaces where the incorrect materials can be removed and replaced with the correct items before the package is sent to the next stage of the order fulfillment process. Having quality control checks baked into your process will help smooth out the entire process, resulting in faster order fulfillment, higher accuracy, and higher profits.
Futureproof With Modular Furniture
Being able to handle the Black Friday surge shouldn’t require having to expand a facility since the increase volume of work is only temporary. Outfitting a packing or distribution center with modular furniture can allow for operations to adapt their existing setup to changes in workload as well as to make improvements to the layout and process.
Treston offers a wide range of modular industrial furniture designed to complement each other in order to create workstations that can be tailored to any operation’s specific needs. Our ergonomic workstations can be customized with accessories including storage bins, rails, cabinets, holders, shelves, panels, lighting, and work surfaces. To promote easy transference of materials between workstations, we have carts in a variety of configurations, including packing carts, bin and cabinet carts, and mobile work surfaces.
Contact us today to speak with a specialist about how to set up your packing facility with Treston modular furniture to help make this your smoothest Black Friday yet.