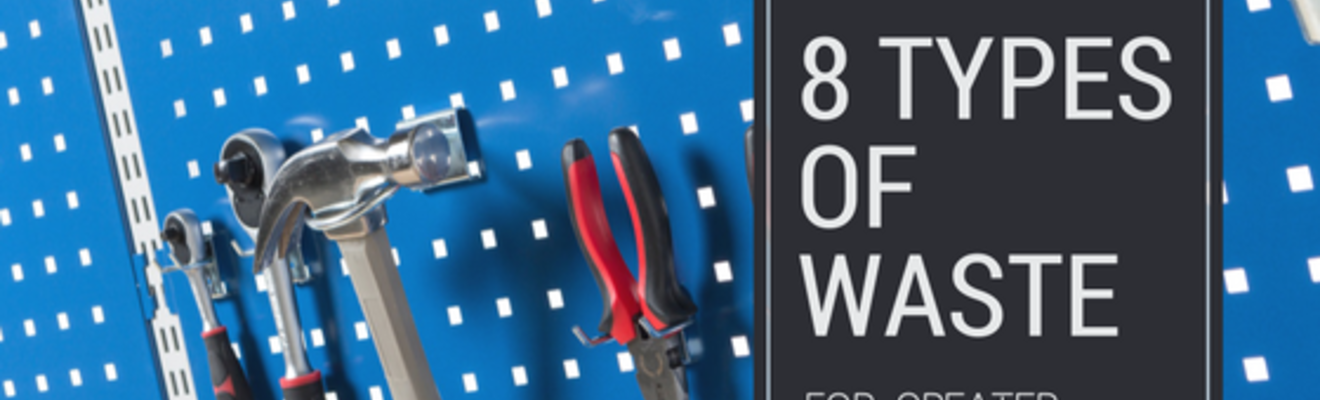
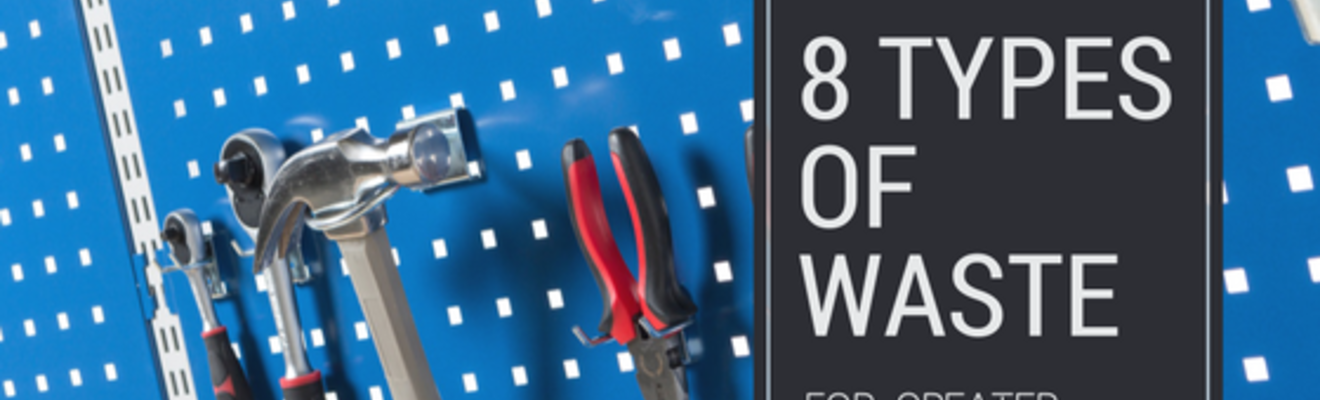
Eliminate These 8 Types of Waste for Greater Productivity
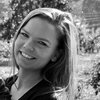
Carissa Harris
Remove Productivity Waste with D-O-W-N-T-I-M-E
Use the acronym "DOWNTIME" below to follow our eight steps for a more productive workplace.
1. D - Defects
Defects include any mistake that requires time, money or resources to correct. This can be caused by several issues, including poor quality control, poor documentation, poor standards, or poor processes. While defects can happen, it is possible to keep them to a minimum by using strict working procedures, utilizing checklists and better understanding work requirements.
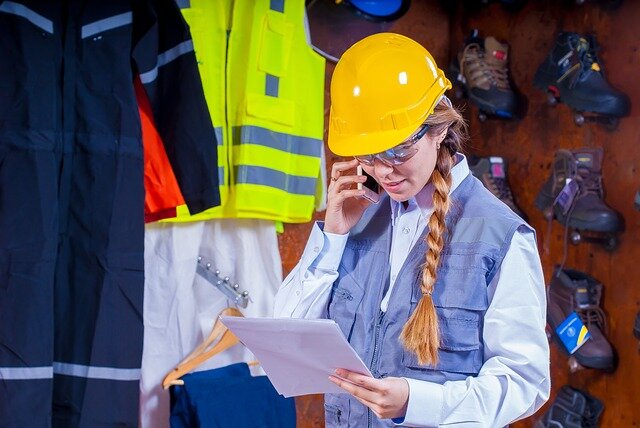
2. O - Overproduction
When product supply becomes greater than the demand for the product, overproduction occurs. This can happen when companies produce to a forecast or are unsure of customer needs, and can cause a significant bottleneck. To overcome this type of waste, it is important to “establish a reasonable work flow”.
3. W - Waiting
Waiting is any pause in work, which can happen for a number of reasons: waiting for approval, broken equipment, lack of supplies, etc. Time spent waiting is money wasted. It is important to prevent this problem by balancing workloads, structure breaks for employees, produce to a forecast, implement proper quality control processes, and communicate effectively.
4. N - Not Utilizing Talent
One of the most valuable assets a company has is talented and knowledgeable employees. When workers are assigned to the wrong task or insufficiently trained, they are not realizing their potential for your organization. “Key solutions include empowering your employees, stop micromanaging, and increase training.”

5. T - Transportation
This type of waste is caused by moving things around. This exists due to poor warehouse layout, extra steps in the work process, and poorly designed systems. This “tends to increase costs, wastes time, and increased the likelihood of product damage and deterioration, and can result in poor communication”. Correct this error by simplifying the work flow, adjust warehouse layouts, and reducing the number of touches on the product.
Shown in this image: An organized workflow eliminates transportation waste.
6. I - Inventory Excess
Inventory excess occurs as a result of overproduction or mismatched production speeds. Identify the source of the problem and establish a reasonable workflow to prevent excess inventory in the future.

7. M - Motion Waste
Motion waste is excess movements that do not benefit the workflow. This could be as simple as an extra arm movement or a wasted trip across the plant for a tool. To correct this problem, keep distances between tools and work to a minimum, eliminate unnecessary steps or arm motions, handle products less often, and simplify the work process. Utilizing ergonomic workstations and carts can drastically reduce motion waste and improve output.
Shown in this image: A mechanic reduces his movements by bringing the tools to the car using a Treston tool cart.
8. E - Excess Processing
Duplicated tasks and poor, lengthy processes can cause excess processing. Examples of this include: excessive reports, multiple signatures, lack of standards, poor communication, and human error. Review your current processes to determine any unnecessary documentation and standardize your processes for more efficient flow. This will eliminate wasted time, money and resources, and empower employees.
Increase Productivity with Organizational Products and Solutions with Treston
Treston has a unique expertise in ergonomic, lean workstation products. To learn more about our lean ideology and how Treston products assist lean environments, click here. We are also here if you have any questions about organizing a more productive workplace, contact us today for direct assistance from our Treston specialists.
Sources:
https://www.processexcellencenetwork.com/business-transformation/article...
http://www.opia.psu.edu/sites/default/files/insights023.pdf