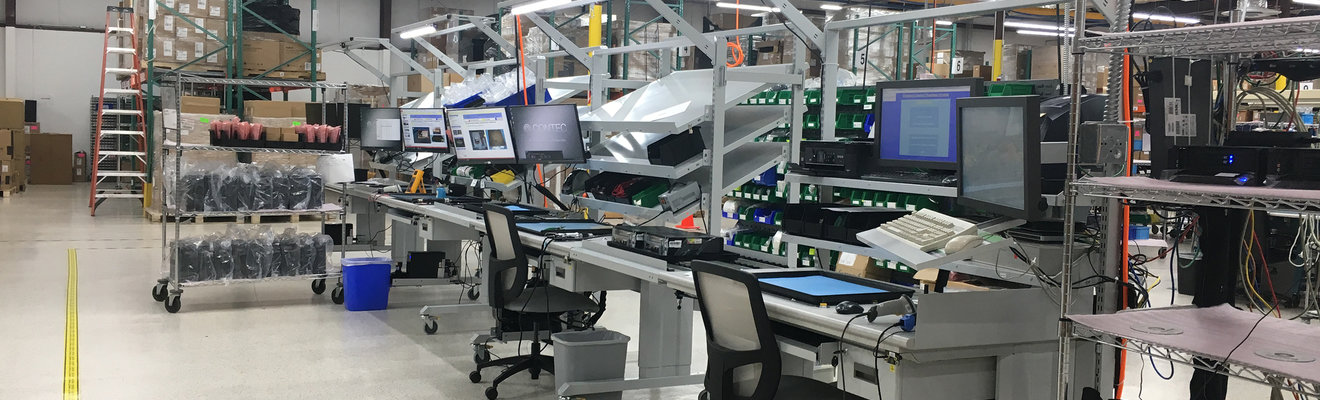
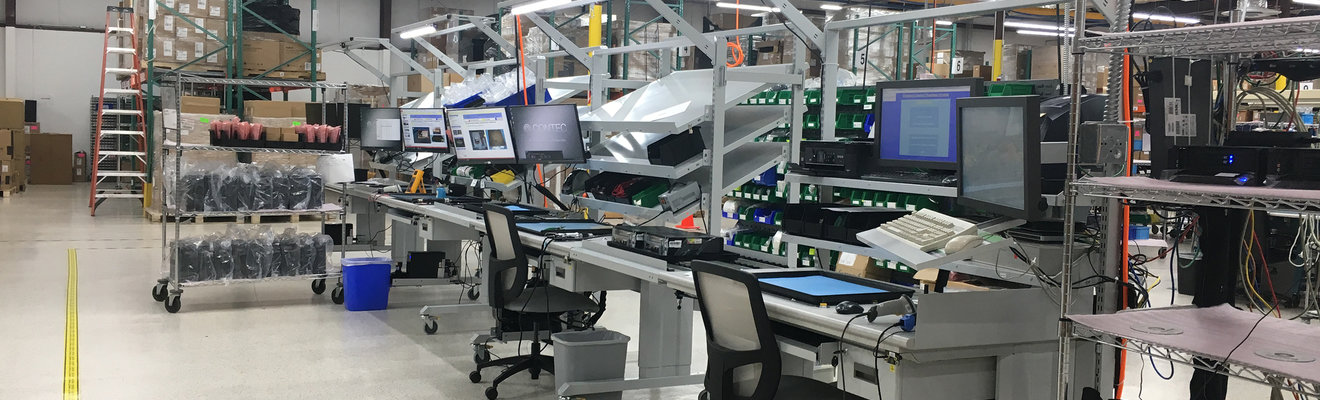
Batch vs. One-Piece Flow Manufacturing
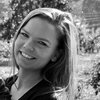
Carissa Harris
Below we will look at the two systems and breakdown the advantages and disadvantages of each.
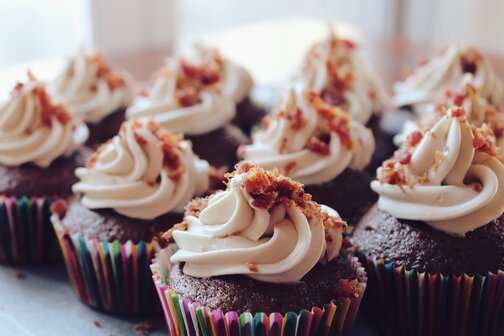
BATCH PRODUCTION
Batch production is the more traditional method of manufacturing, where products move in batches from one step to the next. The process is completed for the entire batch before it can move on to the next step.
Advantages of Batch Production
-
When the initial set up cost of the process is expensive, or requires a long time to complete, running a large batch of products means more items can be produced per each set up.
-
After a batch is completed, they are then transported to the next step. Waiting for a batch to be completed before transporting to the next process means less time is spent transporting the goods.
-
Employees in a batch production system generally find a rhythm when doing one step repeatedly.
-
Batch production is ideal for companies who utilize raw materials that have a short shelf life, such as bakeries.
Disadvantages of Batch Production
-
While more products are being produced in each step, that also means more inventory is required. This extra inventory in the process costs money and takes up space in the line.
-
The downtime for products between steps is inefficient. Products must wait for the entire batch to be complete before they can move to the next step.
-
When a problem occurs in the manufacturing process, the defect will affect the entire batch and may go unnoticed until much further down the production line. Then, the products with defects must be identified and corrected, which can be a lengthy process, especially when producing large batches.
Here is an illustrated demonstration of when defects or mistakes are made and detected in both batch production and flow marketing.

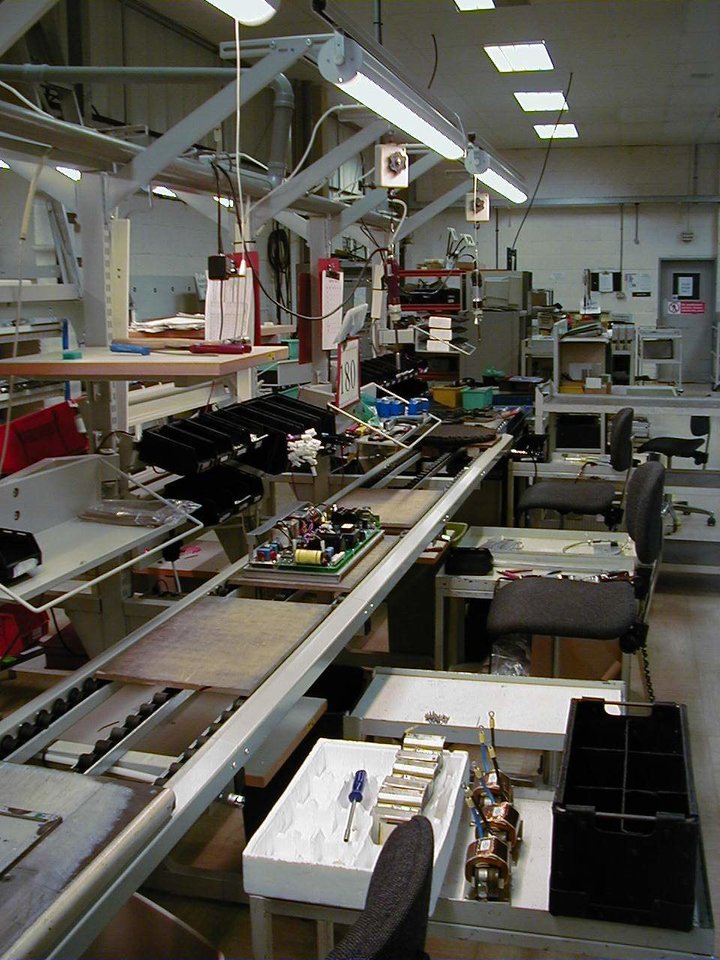
ONE-PIECE FLOW MANUFACTURING
Manufacturers optimizing their workflow have found a system that optimizes the entire production, from set up to completion – one-piece flow manufacturing.
In one-piece flow manufacturing, workstations are arranged so that products can flow one at a time through each step of the process. There is no downtime between steps.
Advantages of One-Piece Flow Manufacturing
-
Reduces inventory – companies are only producing what is needed at any given time. This prevents overproduction or delays in manufacturing. The extra raw material sitting in a batch production line costs money and is not being utilized.
-
In a continuous-flow line, there is less space needed for transporting goods to the next step. With less inventory on the line at each moment, less space and manpower are required for moving products. Each step is optimized and product flow from start to finish with minimal motion. Reduced floor space is especially beneficial when real estate is expensive.
-
The lead time for products to reach the customer is greatly improved. One-piece flow is more efficient and is a great solution for companies looking to improve their customer satisfaction.
-
One-piece flow is often a safer process, due to an optimized layout and less clutter in their work space. With fewer touches comes a reduction in work-related injuries.
-
Improved quality and a reduction in defects – when an issue is detected in a one-piece flow system, it only affects the product in that step. In contrast, a defect in a batch production line will affect an entire batch, or more, before it is noticed. In a continuous flow process, corrective action can be taken quickly with less waste and less time spent locating all products with the defect.
-
With less time needed for production, companies are more flexible in responding to changes from the customer.
Disadvantages of One-Piece Flow Manufacturing
-
One-piece flow will not work well for all companies and processes. Companies with a large variety of products may find it expensive to change their production lines.
-
Implementation involves initial upfront costs. Machines and line layout need to be designed for one-piece production. However, the cost savings of a more efficient production line can greatly outweigh the initial set up costs.
-
Employee morale may be affected if there is no variety in their tasks. Training employees on all processes can help improve their satisfaction.
While one-piece flow manufacturing can cut production time in half, it may not work for every company and every product. A solution for many businesses might be a mix of the two systems, where small batches are produced in a continuous flow format. It is important to analyze your processes and determine the best ways to optimize your operation. Making improvements and adjusting your workflow as needed is important to maintaining a Lean workplace.
The video below shows the difference between batch and one-piece flow manufacturing speeds in real-time, for a visual understanding of this comparison.
All of this is useful information in understanding the differences in flow manufacturing. However, the real truth of their effectiveness is in the results. For an example of one-piece flow in action, our latest customer story proves how Treston products helped Contec Americas increase their manufacturing speed by 30% using half of the floor space!
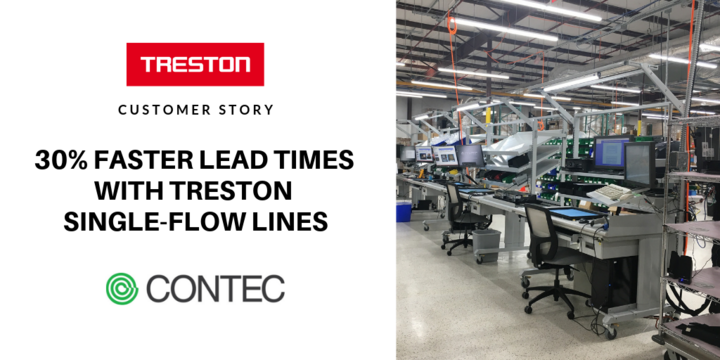
Create the Manufacturing System that Works for Your Business with Treston
When you're ready to get started on building a flow manufacturing process that works best for you and your workspace, the experts at Treston will happily assist! Get started online and design the workstation of your dreams. Our online library of catalogs and brochures will help you understand how to make the most of your workspace with the products we offer. When you know which components you need to purchase, request a quote or contact our team with any questions you may have. We look forward to helping you take the next step forward.
References:
https://www.business2community.com/strategy/one-piece-flow-can-reduce-operations-time-96-01985884