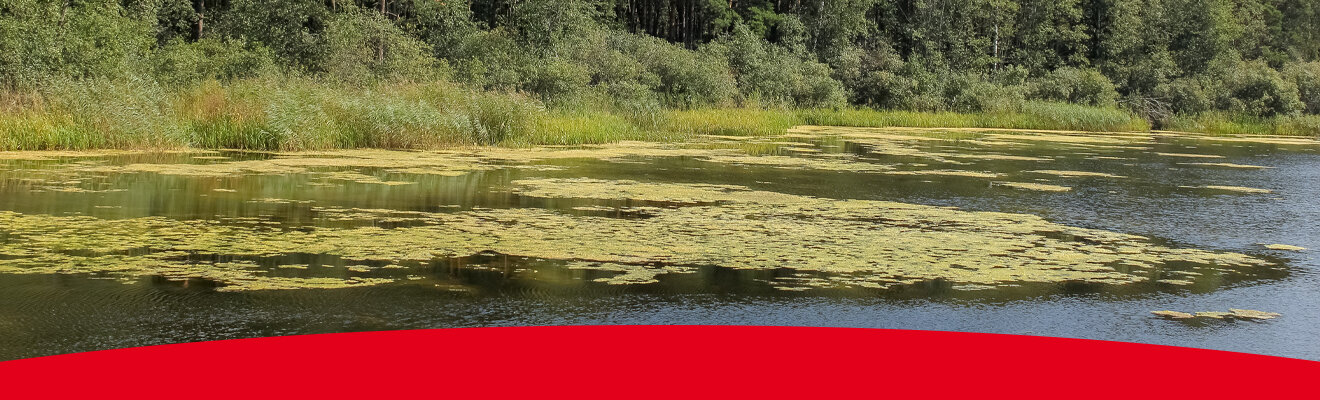
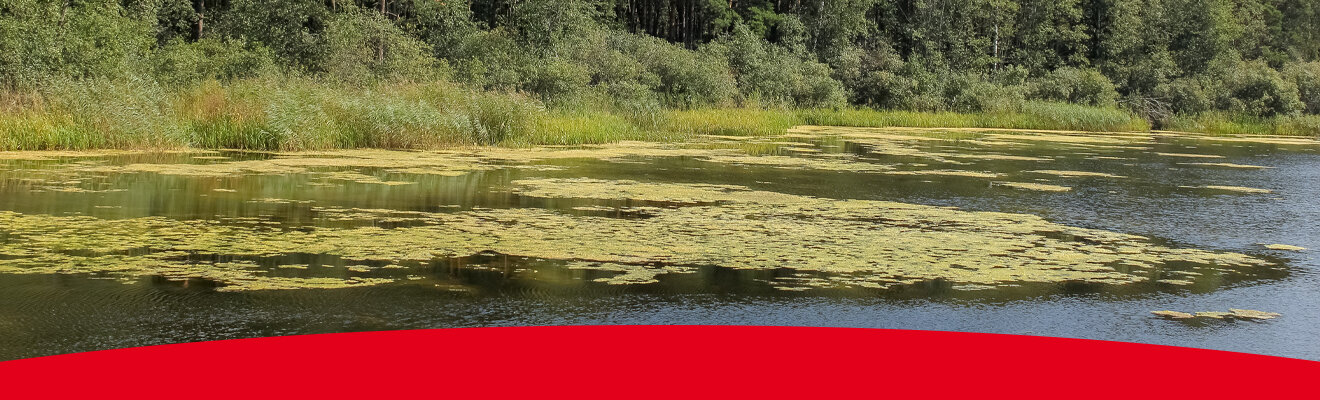
Actions for the environment #1: Ecological Pre-treatment Method
This article introduces the transition of a pre-treatment line to a completely phosphate-free alternative. Phosphates cause eutrophication when ingested. Advanced eutrophication clouds the water and thereby, for example, species typical of the water body are disappearing. Phosphorus (P) is a limited and irreplaceable natural resource.
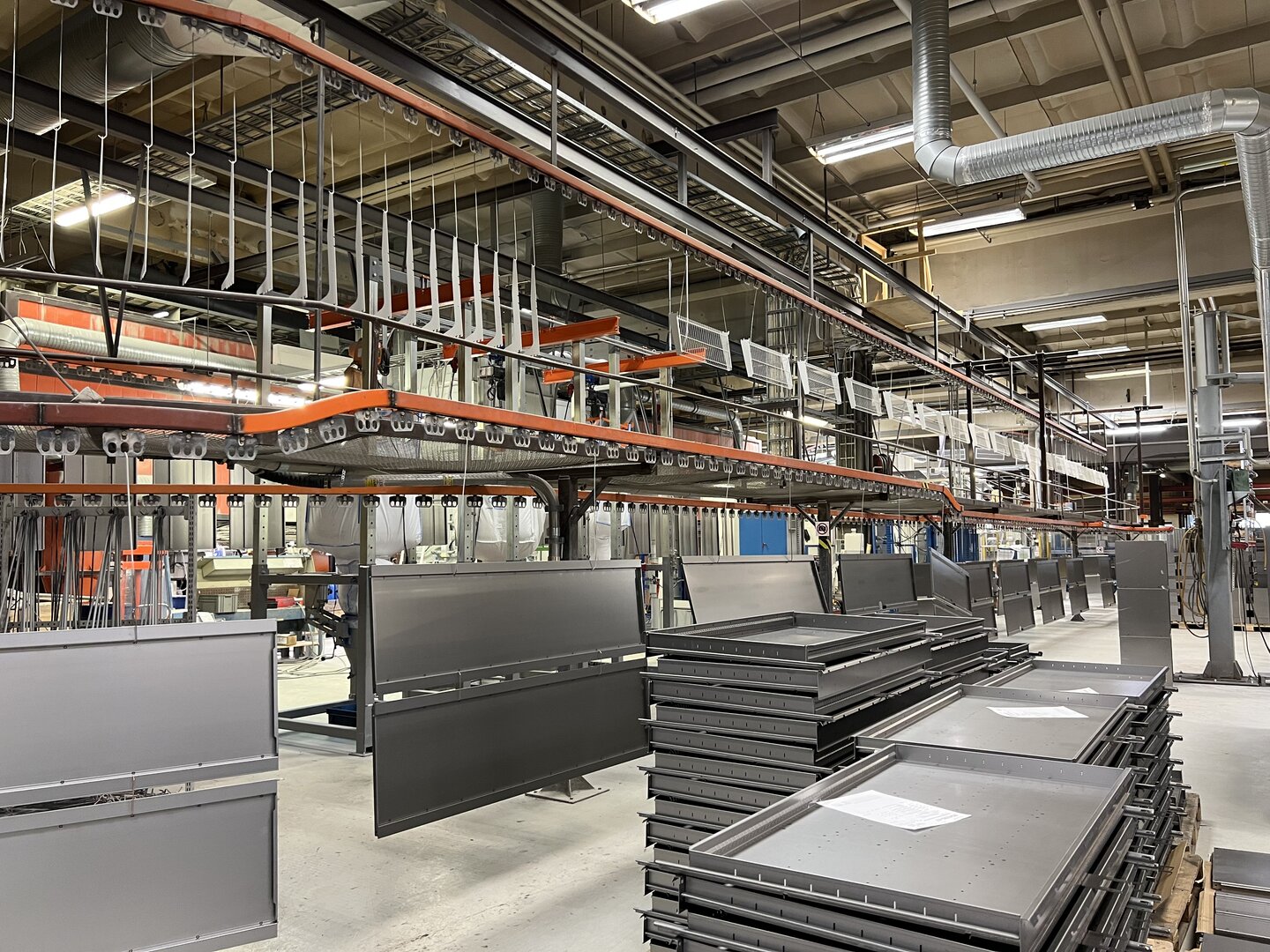
The transition to a more environmentally friendly pre-treatment method
We actively follow different ways in which we could do our part for the environment. At the end of 2021, we moved to a new kind of metal pre-treatment method. A chemical conversion coating came to replace the old iron phosphating pre-treatment.
A new coating to replace the old one
The conversion coating process improves the performance of organic liquid and powder paints, which increases paint adhesion and corrosion resistance. The coating makes a “skin” on the surface, to which the paint adheres effectively.
Pre-treatment process:
- Degreasing wash
- Rinsing
- Conversion coating process
- Drying oven
- Painting
- Paint oven
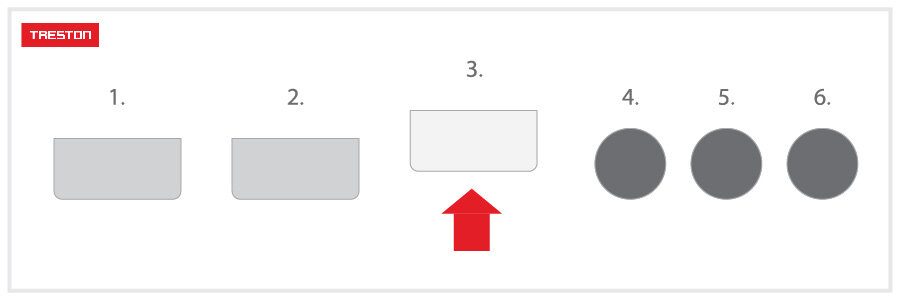
A leap forward in product quality and environmental friendliness
We manufacture products that last and that are guaranteed to be safe to handle. The pieces must not evaporate or dissolve harmful chemicals, and we closely monitor the quality. Plant manager Ilkka Teirioja is happy to say that the new process improves the quality of the products, too: “We didn’t have to change at the expense of product quality. With the new approach, we achieve even better corrosion protection for metal products.”
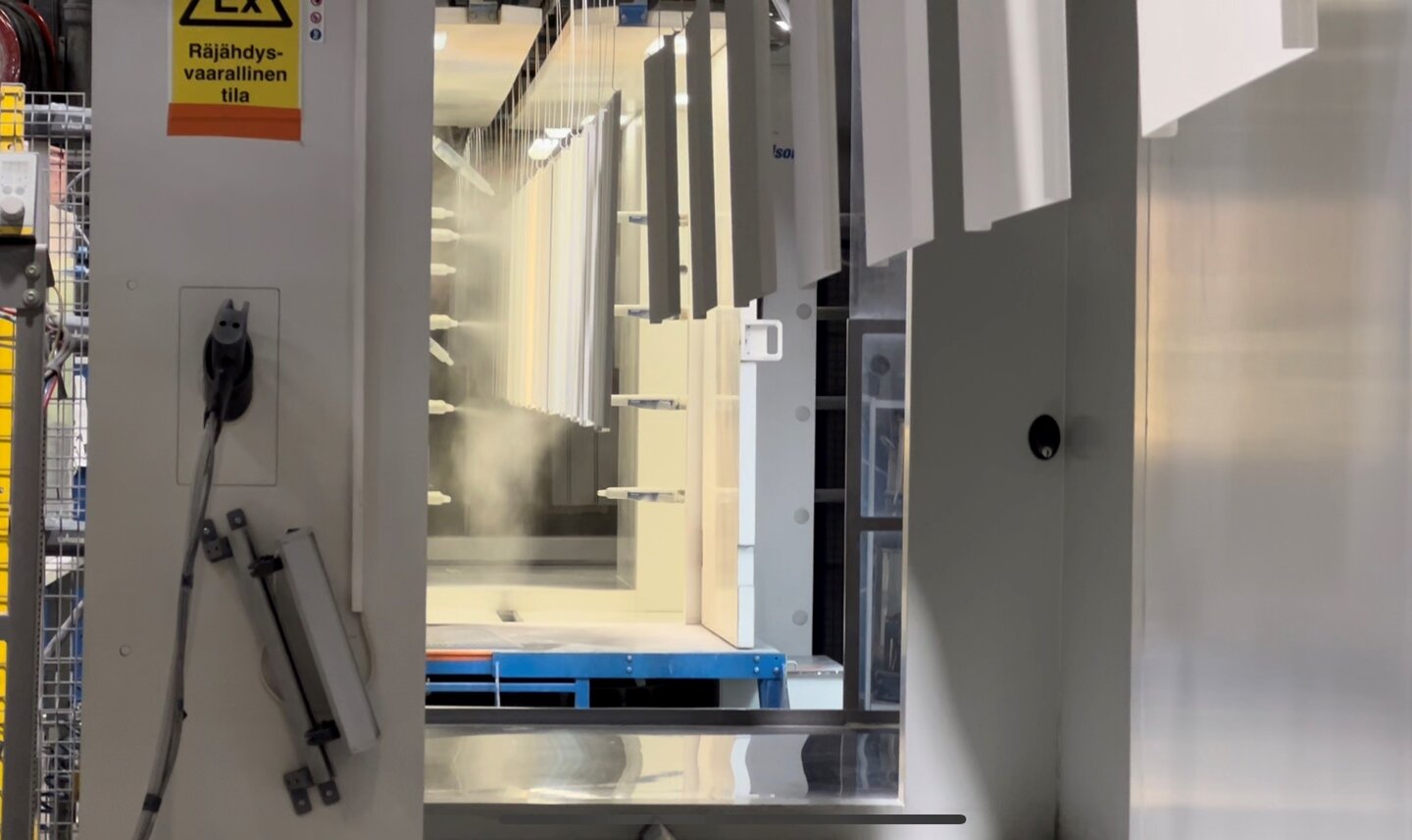
The new method saves the environment and costs
We save phosphates.
The previously used iron phosphating process also improved the adhesion of the paint, but it was rich in phosphates. “The pre-treatment bath was changed 2-3 times a year, and the water was taken to a wastewater treatment plant. In the new process, we will be able to drain the water we use in the future,” Ilkka says.
We save energy.
In addition to the fact that the new pre-treatment process does not contain phosphates or heavy metals, it is also used at a lower temperature than before. “The process temperature for iron phosphating has been 50 to 55 degrees, while with the new method we can operate at 45 degrees. Thus, it has been possible to drop the process temperature by about 5 degrees,” Ilkka states, continuing: “This is a significant way to save energy when the amount of water to be heated is 3 cubic meters.”
We save costs.
“Replacing the washing bath was expensive. If we can drain the washing bath in the future, there will also be financial savings, ”says Ilkka.
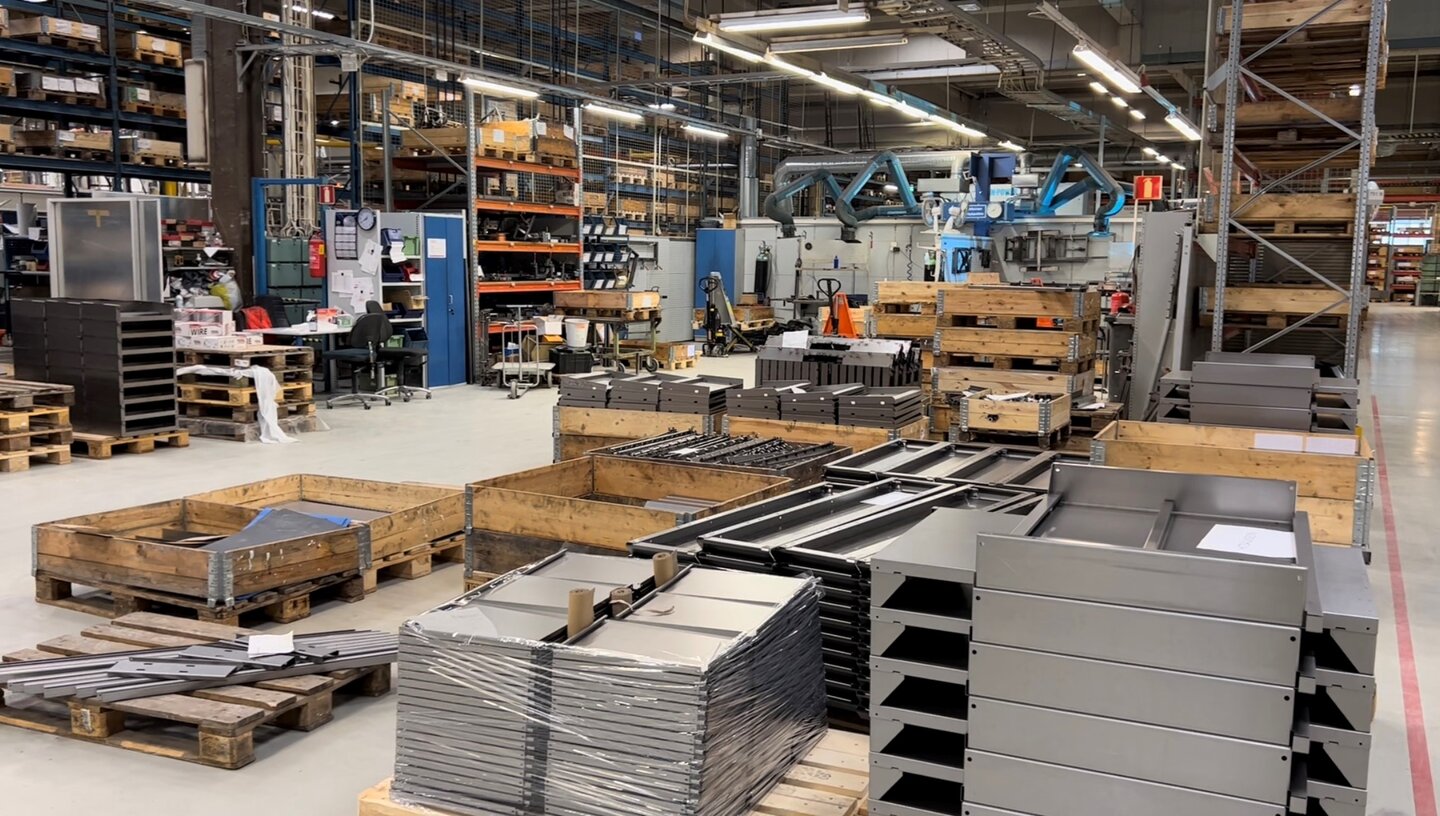
A successful project from which we have learned a lot
According to Ilkka, the project has gone smoothly: “The project has been successful in all respects, and the transition process has been relatively smooth.” Ilkka summarizes the project: “Ensuring employees are up-to-date and learning a new way of doing things has been the most time-consuming part. However, learning new process control routines has already increased our professionalism.”